No, I'm not looking for wiring jobs. ;) Seabob's wiring photos brought back old memories. Back in the '80s I managed an industrial control panel shop and followed some of the jobs to the customer sites for installation and calibration of the instruments. Most of our business was the "air separation" industry. Sucking in air and splitting out the components we wanted such as nitrogen, oxygen, argon, etc.
Most of the steel cabinets we farmed out to a fabrication shop but some of the smaller ones we did the weld up ourselves. I painted all of them with customer chosen colors using Imron.
These are just random pics and not necessarily the same job.
Bare panel freshly painted.
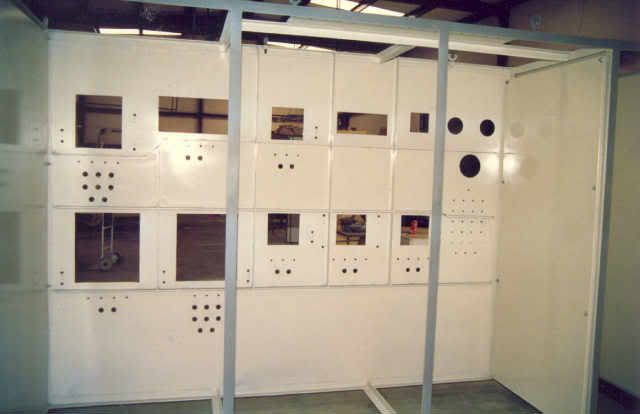
60+ plug-in relays plus some pneumatic instruments wired, tubed, and ready to go. Yes, wire duct makes dressing up the job easier.
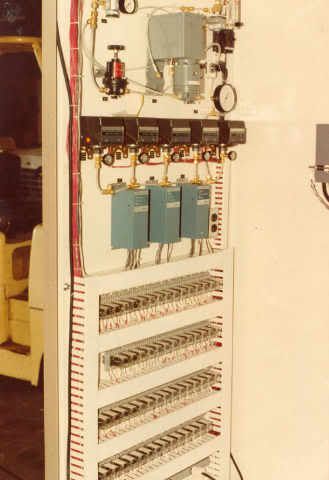
Heavy duty relays and timer.
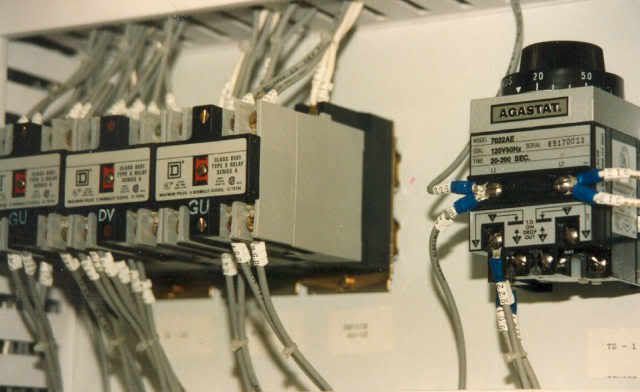
Wires from a controller to terminal blocks. At the plant, wires from devices in the field will be wired to the other side of the terminal blocks.
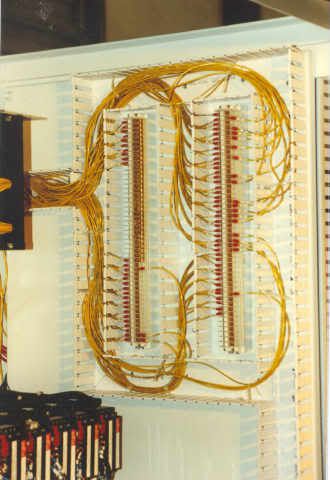
Controls for a 28,000 hp air compressor for a liquid oxygen plant.
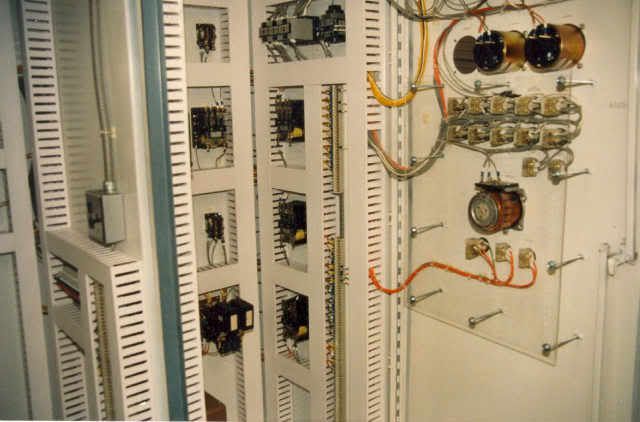
Since we dealt with industrial gasses, all of the product had to be analyzed and certified to a certain percent purity. Rear view of a gas analyzer panel. Hundreds of feet of copper tubing that has to be as neat as the wiring. Believe me, tubing is harder to get neat and pretty than wires. Of course, if you kink it you rip it out and start over. Tubes from the plant carrying gas samples will come in and connect at the top of the panel.
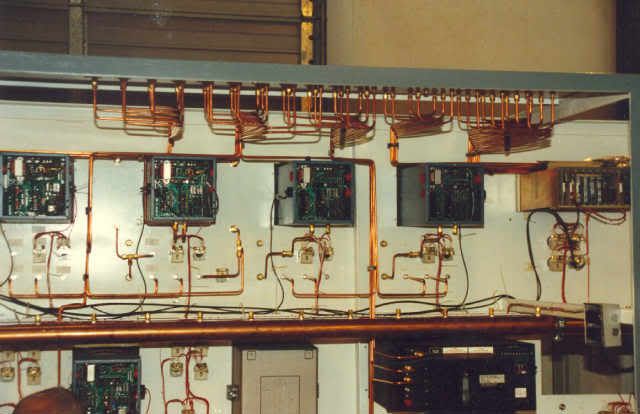
Another gas analyzer almost ready to ship. Just a few more zip ties and it will be ready.

For some real fun, let's make it stainless steel tubing.
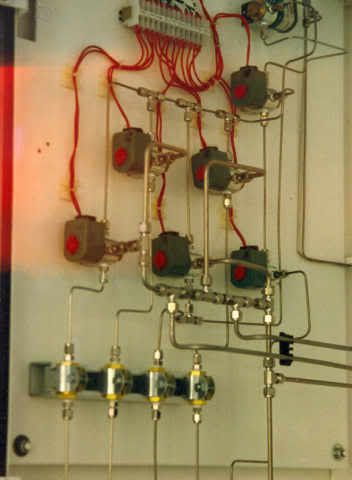
A couple of finished products.
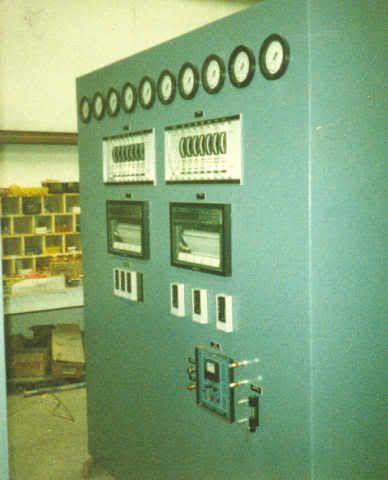
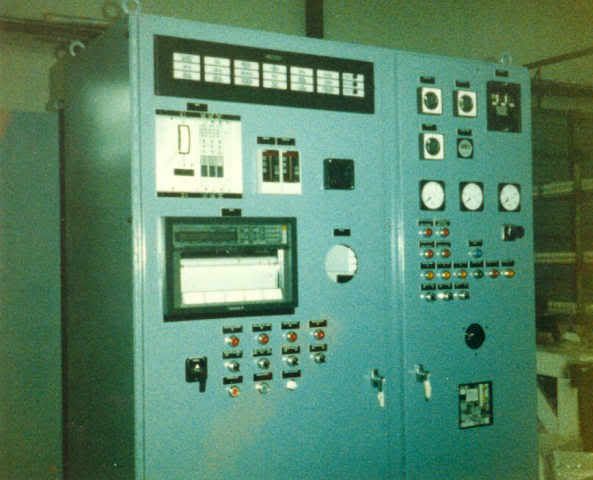
Some of the field work out in a plant. Flow meter station for a nitrogen plant in Baton Rouge.
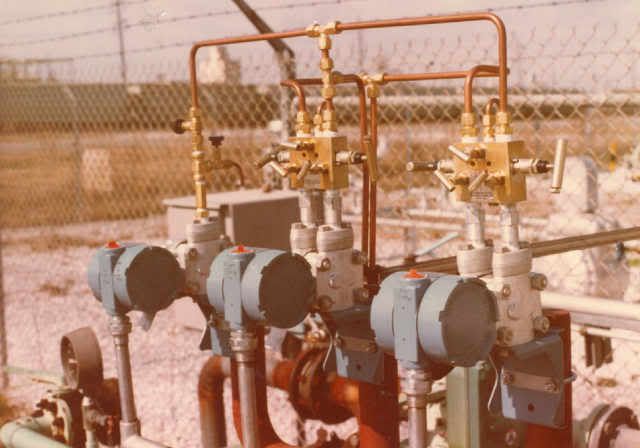
Some of the field work was pretty rough.
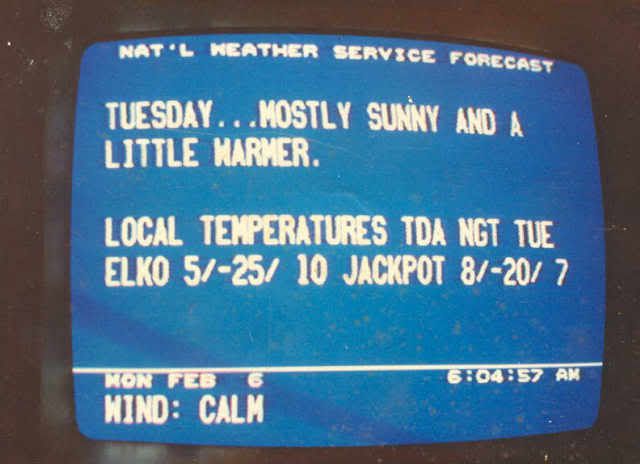